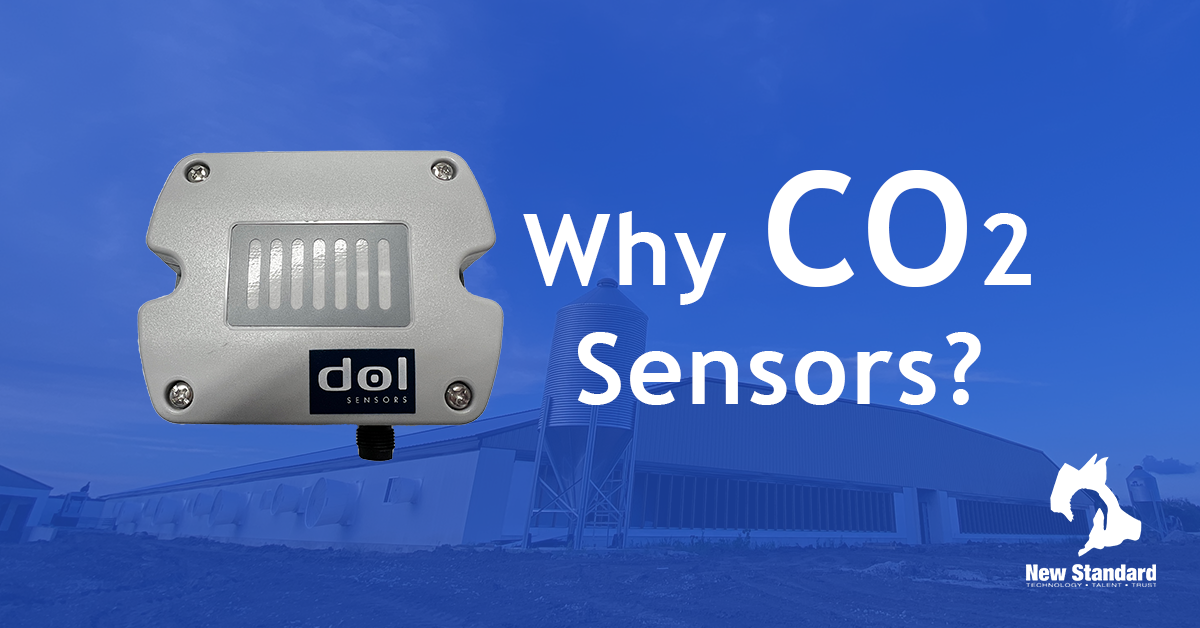
Over the course of the last three years or so, the team at New Standard has started to incorporate a new facet of ventilation regulation (and modification).
Almost every single poultry house that we’ve installed controllers in, now has a CO2 sensor installed and wired to the control .Below, I’ll discuss why this transition is happening and how it may apply to your site.
History
It may be helpful to understand the history of ventilation regulation beyond just temperature. In the past, RH(relative humidity) has been the primary modifier that was used to change ventilation levels beyond temperature rise. For instance, if the temperature in the barn rose, the ventilation typically would rise also. If the RH increased past a certain point, then the ventilation would also rise to lower the RH.
In some houses where the birds are younger, the set point for the heat may have been raised with increasing RH to cause extra ventilation from temperature rise and dry the barn that way. Providing that the heat source could keep up with the added air exchange, the barn would be able to lower the RH quickly. This approach worked well but there was still an inherent lag time to change the quality of the air as it took a bit of time to respond and then some more time to get the humidity levels to drop.
Regulation on CO2
With the advent of more robust sensors and control programming that could better use additional parameters, New Standard started to install CO2 sensors about 2017 and use that feedback to regulate air exchange. What we have found is that the air quality is much easier to keep consistent and the response time is far better as we don’t need to first dry out a barn.For the most part, if a barn is being well controlled for CO2, humidity never has a chance to become a problem.
Obviously, this isn’t perfectly true but when CO2 is regulated, then everything is in a better place.
How we do it
When we set up a new site or a control change, we begin with an understanding of how we want the ventilation to flow or how it currently flows. This, in combination with understanding bird movement will help us place a sensor well. Ambient or atmospheric CO2 is also a good thing to know when setting things up. In South Dakota for example, the ambient CO2 levels range from ~325ppm(parts per million) to 500ppm.
Elevation and time of year will be the primary reasons the numbers shift a bit. We use this as a base of what is desired and then start to increase ventilation levels based on that. To answer an obvious question that may arise (why not measure and regulate on oxygen?), the answer is rather simple. Oxygen sensors are more expensive and require more maintenance which makes them less attractive. By measuring the inverse (dropping oxygen will mean rising CO2), we can stay efficient for expenses and upkeep.There are other questions that arise and things that are good to know. For example, what levels above ambient are considered acceptable, how do birds experience CO2 in a barn setting, and what do I do if I feel the levels are too high?
Let’s start with what is considered acceptable. Acceptable may be a misnomer as that doesn’t always mean the same as “safe”. For instance, concentrations above 1,000ppm will already lead to complaints of drowsiness, concentrations above 2,000ppm can induce headaches, poor concentration and elevated heart rates, and concentrations above 5,000ppm will put you in a place where workplace safety must be addressed. All these levels are safe in the sense that they won’t harm you immediately or directly, but should they really be considered acceptable? I would argue that for the purpose of maintaining a healthy environment, we should target CO2 concentrations below 2,000ppm. This may not always be possible, but we should strive for that goal.
Birds do have a higher tolerance for hypoxia (lowered blood/oxygen levels) as they are still designed to exist at altitudes that humans don’t naturally travel. That doesn’t mean it doesn’t affect them; it just means they can tolerate it better. It is still advised to maintain a level of CO2 that is preferred for humans knowing it will be beneficial to the birds as well. Now, if the levels do start to rise, we’ll program the control to respond accordingly. Typically, we’ll start increasing ventilation levels once the ppm gets above 750. As barn sizes are all different, the level of increase for airflow will have to fit that barn. We would need to understand what is possible for increased ventilation without cooling the barn below the set point and then set the upper limits of correction to be reached by the time we hit 2,500ppm. In most cases, I recommend an aggressive approach by the time we reach 2,000ppm.This may be a new topic for some, and to others, they’ll freely attest to the benefits.
Danny Waldner (turkey manager,Platte Colony) just relayed to me personally that the ability to control his air quality is far better now that he can monitor and regulate CO2. Of course, we’d like to think he also benefits greatly because we’ve installed a new Fusion controller for him a couple months ago.
If you’re in need of a better understanding or if you want to look at what can be done to make your site better, give us a call; we’d love to give you the same story Danny has.
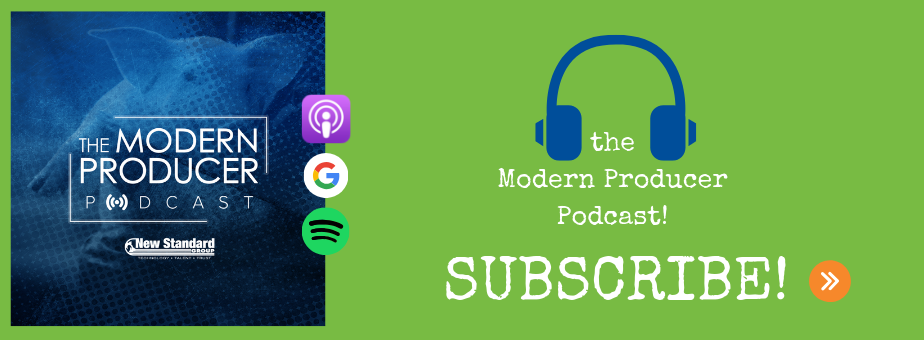